2017/12/08
Newly Developed Industrial Network Achieves New Manufacturing Using IoT and AI
MECHATROLINK MEMBERS ASSOCIATION
October 17, 2017
Newly Developed Industrial Network Achieves New Manufacturing Using IoT and AI
- Synchronization and Linkage between Motion Data and Sensor Data with MECHATROLINK-4 and Σ-LINK II -
The MECHATROLINK MEMBERS ASSOCIATION (MMA, headquarters in Iruma, Saitama Prefecture), which promotes MECHATROLINK, an open motion network developed in Japan, announces that Yaskawa Electric Corporation has developed the new-generation industrial open network technologies MECHATROLINK-4 (M-4) and Σ-LINK II.
In addition, MMA has transferred this newly developed technology from Yaskawa Electric Corporation and is in preparation to release the MECHATROLINK-4 specifications. The unveiling is scheduled to take place at the Yaskawa Electric Corporation booth and the MMA booth at System Control Fair 2017, to be held from Wednesday November 29, 2017 to Friday December 1, 2017 at Tokyo Big Sight.
- Aims of Development
The MMA used MECHATROLINK-III (M-III, released in 2007) to reduce wiring and improve productivity by improving the functionality and performance of manufacturing equipment, and also to respond to demands such as the improvement of maintenance through networking.
In recent years, the environment for industry is changing significantly. An example is the introduction of smart production and operations, along with the achievement of flexible and stable production using IoT and AI. A variety of sensors are being used to ensure product quality and achieve predictive maintenance on machines and equipment at production sites, and the data generated by these sensors needs to be collected and utilized.
In order to meet these needs, the MMA board committee has studied the specifications for the new generation of industrial network technology and has developed the specification of M-4 as the optimized network for motion control and the Σ-LINK II to connect sensors and I/O devices. Using the newly developed M-4 and Σ-LINK II together, it is possible to acquire not only motion control related data but also various sensor data synchronously and easily. This further raises productivity and achieves aligns existing systems with the standards of New Manufacturing utilizing the IoT and AI. - Summary of New Technology
In addition to maintaining the high functionality, high performance, high reliability, and usability of the previous M-III (ensuring the application’s compatibility), M-4 improves transmission efficiency (performance improvement of about 4x under the same conditions), provides much higher functionality and performance by supporting distributed systems with multi-master functions, and achieves simpler development and maintenance.
While inheriting the high functionality and high reliability communications of previous Σ-LINK encoder communications, Σ-LINK II supports cascade connections like MECHATROLINK. Σ-LINK II achieves higher functionality and performance with reduced wiring by connecting not only encoders, but also sensors, I/O equipment, and other devices installed on the machine side in cascades.
Also, combining M-4 and Σ-LINK II makes it possible to easily achieve much higher functionality and performance through synchronization and unified control of motion data and sensor data. - Specifications and Features
- 1) M-4 Specifications and Features
Layer Item M-Ⅲ M-4 Application layer Command profile Standard servo, standard stepping motor drivers, standard I/O, standard inverter Data link layer Maximum number of stations C1 master 1 station,
C2 master 1 station,
slave 62 stations128 stations
(Maximum 8 masters, Maximum 127 slaves)Sync manager Not supported Supported Sync jitter ≦±1μs (Limit of 19 hops maximum) ≦±1μs Multi-master Not supported Supported Communication with multiple transmission cycles Not supported Supported Duplex Half duplex Full duplex Internet protocol Not supported Supported Ethernet compatibility Only PHY layer
Compatible
Physical layer Transmission speed 100Mbps 100Mbps(M-4)/1Gbps (M-4G) Alternative Transmission distance 100m between stations 100m between stations (100Mbps)
80m between stations (1Gbps)Topology Cascade/star - ①Application Compatibility
- ・Secures application compatibility with M-III
- ・Hardware can be shared between M-III, M-4, and other networks through multi-protocol communication ASICs
- ・M-4/M-III gateways enable to connect (synchronize) with M-III systems.
These features make it possible to simply shift from M-III systems to M-4 systems.
- ②Improved Usability Through Improved Transmission Efficiency
- ・Approximately 4 times the number of nodes are possible with the same connection environment
- ・The transmission cycle can be set separately for each slave. This increases the degrees of freedom for system design and enables optimization.
- ③Support for Distributed Systems through Multi-Master Functions
- ・Multiple masters can be set up in the same network. Simultaneous parallel execution of processing between masters makes it possible to synchronize all devices without lengthening transmission cycles and makes construction of distributed systems easier.
- ④Network Safety Support
- ・Safety systems can be constructed in the same network
- ⑤Support for General-Purpose Ethernet
- ・PCs, visual devices, and other general-purpose Ethernet devices can be connected.
- ①Application Compatibility
- 2) Σ-LINK-II Specifications and Features
While inheriting the high functionality, high reliability communications of previous encoder communications (Σ-LINK), Σ-LINK II supports cascade connections like MECHATROLINK. Σ-LINK II achieves more advanced functionality and higher performance with reduced wiring by connecting not only encoders but also sensors, I/O equipment, and other devices installed on the machine side in cascades.- ①Reduced wiring
- ・Reduced wiring is achieved by sharing sensor signals with the motor encoder
- ②Unified control of sensor data and motion data (data synchronization)
- ・Higher functionality can be achieved by taking in sensor signals at higher speed, and sensor data and motion data can be synchronized by linking with MECHATROLINK.
Layer Item Σ-LINK Σ-LINK Ⅱ Application layer Profile Σ-LINKcommand profile Data link layer Transmission mode Cyclic transmission,
Acyclic transmissionMaximum number of slaves 1 14 Duplex Half duplex Physical layer Transmission speed 4Mbps/8Mbps 4Mbps/8Mbps/16Mbps/
24Mbps/32MbpsElectrical specification RS-485 Network topology Peer-to-peer(one-to-one) Peer-to-peer (one-to-one),
cascade(one-to-many)
- ・Higher functionality can be achieved by taking in sensor signals at higher speed, and sensor data and motion data can be synchronized by linking with MECHATROLINK.
- ①Reduced wiring
- 1) M-4 Specifications and Features
About the MMA
Japanese name: MECHATROLINK Kyokai
English name: MECHATROLINK MEMBERS ASSOCIATION
Abbreviation: MMA
The MMA was established in January 2003 to promote MECHATROLINK as an open field network technology. The MMA comprises of eight board committee companies, MECHATROLINK product developers and MECHATROLINK users. As of the end of September 2017, the association comprises 3066 companies. Branch offices have been established in South Korea, China, Taiwan, the United States, Germany, India and ASEAN. These offices provide support for worldwide MECHATROLINK promotion activities as well as MMA member support.
Members of the Board Committee
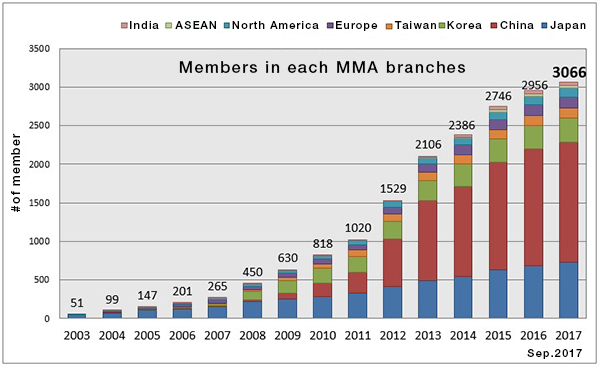
MMA Membership as of Sept. 30, 2017
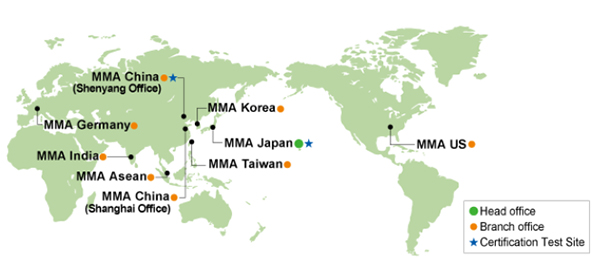
MMA Global Support System
※ Ethernet is a trademark of Fuji Xerox Co., Ltd
MECHATROLINK MEMBERS ASSOCIATION
Head Office Representative: Takuya Miwa
Address: 480 Kami-Fujisawa, Iruma, Saitama, Japan
Website: http://www.mechatrolink.org